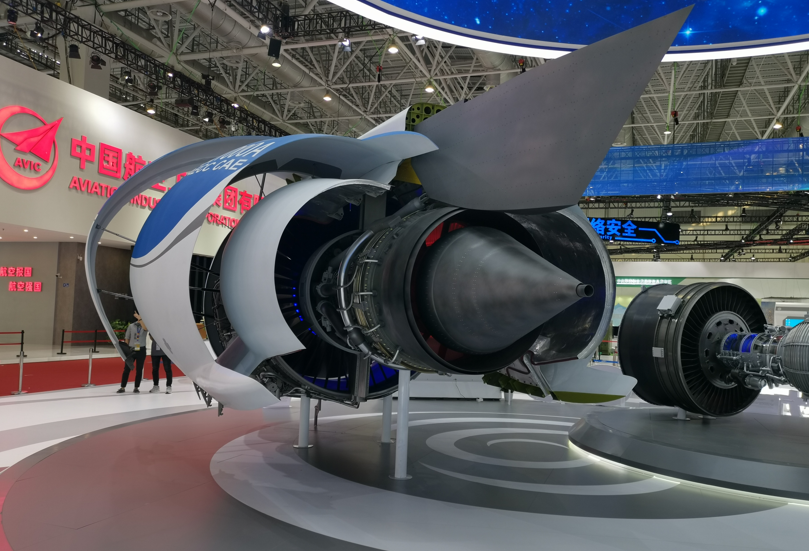
中国航空发动机集团简介、直属单位与主营业务
2022年04年24日
中国航天科技集团有限公司 2024-12-31
“我们成功了!”航天科技集团七院7102厂表面处理车间电镀现场,几名员工围着刚电镀出槽的产品零件欢呼。大家不禁感慨:这两年吃过的苦受过的累,值了。
无氰电镀势在必行
消息很快传遍了整个表面处理车间。
小小的零件何以引起这么多人关注?其实关注不在零件本身,而在于它“穿衣”过程中电镀工艺的改进。
对电镀行业稍有了解的人都知道,传统的电镀是有氰电镀,即有氰化物为络合剂的电镀,具有镀层均匀、结合力好、镀液分散性能和覆盖能力好等优点,对产品的耐腐蚀性能、外观装饰性能的提高有着重要作用,这也是一直以来氰化电镀作为航天型号产品制造的重要工艺技术之一的原因。
然而,氰化物作为剧毒物,其致死量仅为0.06克。操作者在电镀过程中,槽液还会产生极少量的氰化物气体,其危险性不言而喻。
“工厂采取了系统的严防措施,虽从没发生过中毒安全事故,但它始终是一个让人高度紧张的隐患。”表面处理车间党支部书记、无氰电镀工艺攻关负责人朱小玲说。
正因为氰化物对环境和人体的危害性极大,国家将其作为管制物品,从生产、销售到使用范围,都有着严格的规定。
据介绍,该车间以前每次需要氰化电镀时,都是至少提前1个多月向公安部门提出申请,通过各相关部门近20个流程的审批,最后在当地公安部门派专人现场监督下,药品才能加入电镀槽内。该厂房也被列入了I级危险点,除配置专门的监控设施外,还必须配备2人24小时在生产现场安全巡查,每年需为此支付20多万元。此外电镀产生的污泥也必须经专业机构作特殊处理,每年费用也需10多万元。因此,无氰电镀替代氰化电镀势在必行。
识势而动蓄势待发
2022年工厂将无氰电镀工艺攻关列为重点项目,将该任务下达到表面处理车间。
接到任务后,车间当即成立了以电镀工艺技术人员、操作者为主的无氰电镀工艺攻关组,在确定项目负责人时,一个小伙子举手问道:“我可以吗?”大家有些惊讶地看着这个年轻人,而朱小玲和车间主任周洁不约而同地回答:“可以!”事实证明,这个名叫林少凯的年轻人没有辜负大家对他的信任。
“小伙子(林少凯)研究生毕业后,在多个单位干过,有一定的经验。他是2021年初应聘到车间的,我们多次与他就电镀工艺和表面处理新材料研究进行了交流,感觉这小子肚里有货。”朱小玲说。
作为项目负责人,林少凯给自己定下了“只许成功,不能失败”的目标。当晚回到家,连晚饭都顾不得吃,就查询起无氰电镀相关资料……整整1个星期,除了吃饭睡觉,没出过房门半步。
无氰电镀工艺研究的关键点在于电镀液的配制,只有先研究出配方,才算是踏出项目研究的第一步。而电镀液原材料的选用又是配方的关键。从海量的数据中遴选出满足无氰电镀层的制造要求的原材料,个中滋味只有林少凯自己知道。
原材料初选后次日一大早,他背着行囊先后奔赴北京、武汉、重庆、贵州等地,实地调研厂家生产的原材料性能、试验指标,同时又分别与5个厂家取得联系,现场考察原材料的应用情况。连续3个多月,他不是在实地调研,就是在调研的路上。“没有亲眼看到和见证,只看纸面上的说明介绍,始终让人不放心。”林少凯说。
打造无氰“有情”配方
原材料到位,如何调制出无氰电镀液呢?无氰电镀液配方并不是简单地将原材料按比例融合在一起,还要研究与之相匹配的温度及电流密度的最佳值。
如何才能获得各原材料比例及温度、电流密度的最佳参数值?林少凯提出的“单因素试验+正交试验”法,得到项目组的一致认可。
说时容易做时难。项目的一个分项实验需做七八次甚至十多次,一次实验耗时三四个小时甚至更久。整个项目共七八十个分项,实验总次数就得七八百次,按每天10小时计算,那也得要1年多。为缩短实验周期,林少凯几乎全泡在实验室。
实验中,他们的眼睛始终盯着数据的变化,生怕漏看一个细节。三四小时的实验下来,腰酸背痛不说,眼睛还胀得几乎睁不开。
就这样,在不到1年的时间,林少凯和他的项目组圆满完成了实验,不仅获得了各项参数最佳参数值,还摸索出了解决无氰电镀工艺稳定性问题的试验法、解决无氰电镀中产品氢脆问题的调整法、解决重金属杂质污染难题办法等研究成果。
实验成功,随着一个个参数值出炉,后面的生产线改造、模拟批产试验就简单多了。他们提前3个月生产出第一批无氰电镀产品,经检测,镀层外观、镀层深度、镀层耐蚀性等各项指标符合标准。
据介绍,无氰电镀工艺的掌握,不仅消除了氰化电镀对人体、环境危害隐患,而且每年可为工厂节约30多万元。
(曾令川)
2022年04年24日
2022年04年20日
2019年12年07日
2023年03年18日
2019年12年13日
2019年12年11日
2022年08年01日
2019年10年05日
2019年12年12日
2022年04年12日
评论 (0)